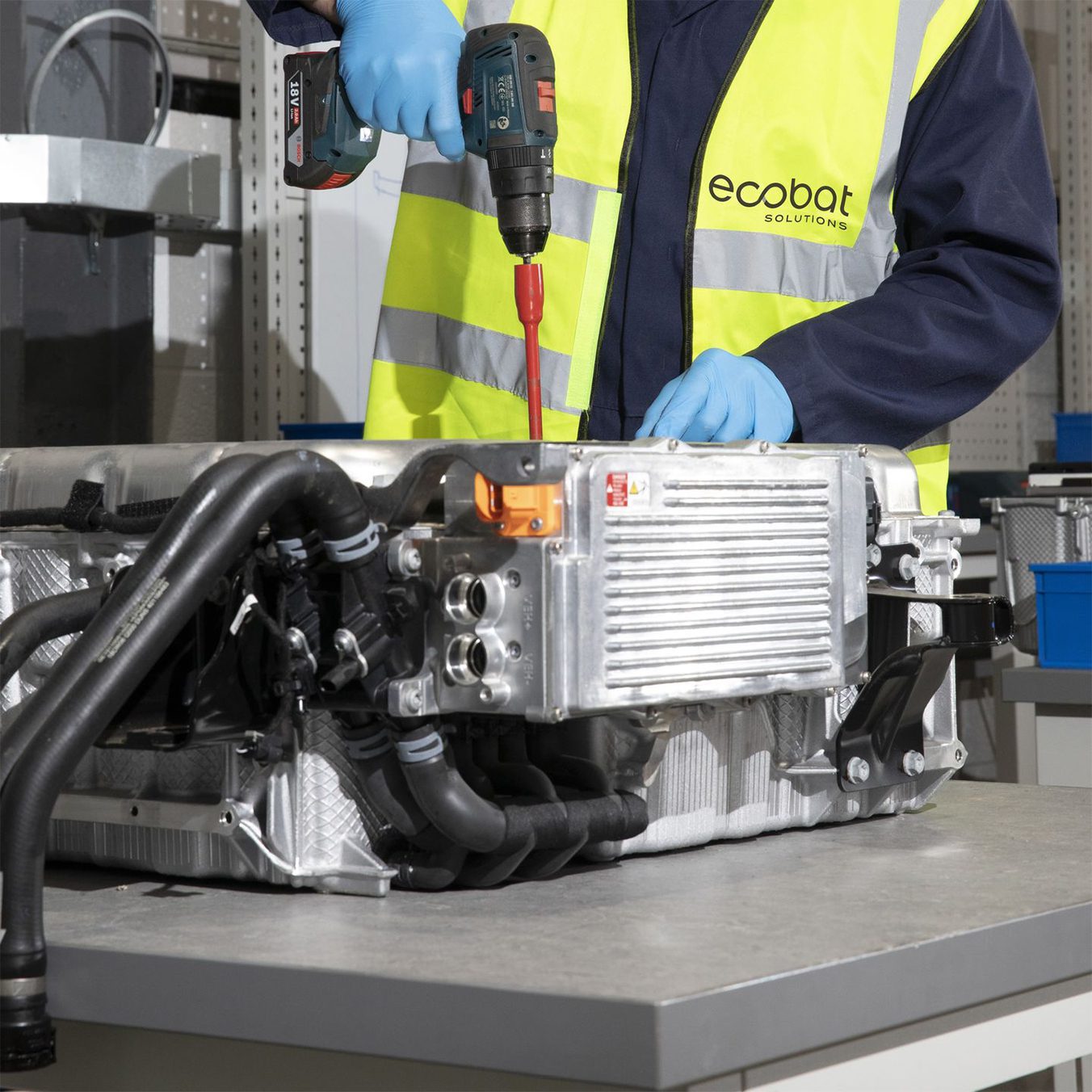
What happens to lithium-ion batteries when they are recycled?
Ecobat | August 30, 2024
Lithium-ion batteries are incredibly energy dense, useful components which enable expanded electrification of virtually every mobile application. It seems like every year, new uses, expanded capacities and lower cost options reach the market – but not without significant engineering investment. These marvels of modern material engineering consist of very specific blends of critical materials, including lithium, cobalt, nickel and manganese. When a lithium-ion battery has reached the end of its useful life, the best home for it is a closed loop recycling facility which can safely and efficiently return these critical materials back to battery manufacturers for reuse in new advanced batteries.
How to tell if a battery is ready for recycling?
Everyone’s had the frustration of an older cell phone slowly losing battery capacity until it seems like you’re charging it for as long as you’re using it every day. The same thing happens with every other battery today, including large format lithium-ion batteries. Through various failure modes, batteries slowly lose capacity until they reach a point, they are no longer appropriate for their given application – typically, this is when a battery should be sent to a recycler. This capacity is referred to as “state of health,” and is defined as the current energy capacity of a battery divided by its original design capacity. There is no clear-cut definition for when a battery reaches “end-of-life,” but most applications demand batteries have a capacity of at least 70-85% of their original design.
What alternate paths are there and why is battery recycling generally preferred?
So, shouldn’t we be using the remaining 70-85% of a battery that’s left when it’s reached its original end-of-life? Sometimes, but not often. Some critical application batteries (such as those used in medical devices, critical network backup power, etc.) have such a high threshold for state of health that it is very straightforward to pull cells for another application. However, several factors make reuse and second life unappealing. First, most applications have a relatively high state of health- if you’re building a battery energy storage system (BESS), you don’t want to start with a reduced capacity, even though this is the traditional path for second life batteries. Indeed, state of health is not linearly correlated with performance – full power supply, thermal response and other factors are impacted by reduced state of health.
Next, with the rapid development of new battery technology, it’s not necessarily true that a second life battery can be sourced for a lower cost per kWh than a new battery. When looking through the spectrum of total cost of ownership (TCO), many times we see that new batteries coming onto the market today have such significant performance and durability improvements, there’s a more positive value to new batteries than reused ones.
The final major category is liability risk. When a battery is repurposed, it is reengineered with new controls, components and is utilized in a different application with different cycles and performance requirements. Ultimately, who is responsible for the performance of this second life battery? And if the original designer had their way, would they want the brand exposure of a potential incident with their battery, regardless of who is responsible?
The path towards a sustainable end-of-life process for advanced batteries is complicated and certainly not defined, but a responsible choice will always be to recycle end-of-life batteries with a reputable battery recycling firm like Ecobat.
What is the process a battery goes through when it’s recycled?
When recycling, the first stage is battery collection - making sure that battery is harvested from its original application and bound for a recycling facility. Next is sorting – battery recyclers derive value from the critical materials inside that battery, but not all lithium-ion batteries contain each material. By sorting the different cathode chemistries, recyclers maximize their ability to recover value from the scrap, the key to building a self-sufficient, closed loop recycling industry.
Once sorted, batteries are shredded and run through material separation stages to ultimately produce “black mass.” Black mass is the reacted and separated active electrode material present in each battery. Black mass contains nickel, cobalt and lithium which drives the recycling business. The black mass recovery and recycling process is performed by a “pretreatment” recycler.
Black mass is then sent to a high-volume refiner which recovers the nickel, cobalt and lithium to a battery grade. This refining is typically done through a hydrometallurgic or pyrometallurgic process. From there, the battery grade material (generally a sulfate, hydroxide or carbonate) is sent to a cathode active material (CAM) precursor manufacturer, who creates the feedstock for CAM manufacturers from both recycled and virgin mined materials. Once in CAM form, the material is sent to a cell producer who uses it to make new batteries.
Is there any difference between a new battery made of recycled components versus virgin mined materials?
The biggest difference is that you don’t need to open a mine to get the recycled material. Once the black mass has been chemically converted into sulfate, there is no practical difference in material.